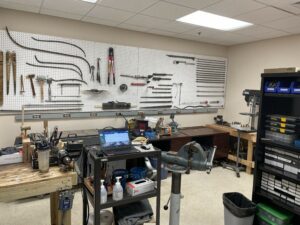
In the interior of the Music Building, at the end of one of the hallways on the ground floor is Room 263—the Instrument Repair Shop. The room is set up with an L-shaped bench full of screwdrivers, pliers, rawhide mallets, tweezers, and spring hooks. There is also a detachable cart, which serves as a mobile repair unit. Storage shelves house spare parts. One area of the room is designated for string maintenance items like sound post setters, files, and peg shavers, while another area houses ultrasonic brass cleaning equipment. Then there is the heavy equipment: drill press, belt sander, grinder, lathe, and buffing machine.
If it feels like a triage center, it is, only this one is for musical instruments. And at the center of it all is the “surgeon”—Jon Goodman:
“I mostly run what is known as a ‘play condition shop’ down here. I see about 100 instruments a semester for anything from quick checks, cleanings, replacing a pad here or there to replacing corks, resetting bridges or sound posts. My job is to keep instruments in students’ hands as much as possible. With classes, rehearsals, and performances, there’s not much time that the instruments can stay in the shop.”
A typical day for Goodman involves instrument check-outs, check-ins, and repairs. This can be anything from checking out a professional model instrument to a student who hasn’t yet purchased their instrument, assigning a secondary instrument for a student to use in ensembles, or assigning student-level instruments to future music educators. A checkout usually includes doing a quick assessment before the instruments go out and making sure they have the accessories they need. And in between, he does the repairs.
Goodman is responsible for taking care of the school’s inventory of over 600 instruments—all of them except the pianos—which are handled by the school’s other technician, Stephen Duncan.
Goodman says the most interesting repair work he’s done has been here at CVPA where he first put his hands on some eastern music instruments:
“I’ve spent some time re-stringing the sitars and sarod. I had never worked on these instruments anywhere else, but our Indian Ensemble Teacher, Gorang Doshi, has been really helpful in guiding me. It’s been so interesting to understand more about them. It’s always fun to get something you have never seen before and see when it was made and figure out the intricacies of getting them back into working order.”
What happens to instruments that don’t make it through “surgery?” Goodman says they find a final resting place but in a different form:
“If an instrument can’t be repaired, typically I keep it for parts if we have other instruments in our inventory that are the same make and model. If we don’t have like instruments, we surplus these items, and they get sold at the next surplus auction. If I know it is something that could be used (like parts for old Conn saxophones, or other sought-after models), I’ll give other technicians a heads up so they can use it.”
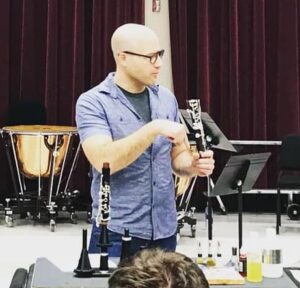
In addition to his position as Instrument Repair Technician at CVPA Jon also runs his own repair business, Goodman Customs Woodwinds. Specializing in clarinet repair techniques, Jon has given clinics at Appalachian State University, Duke University, and UNC Greensboro. Jon is also an active performer as a new music chamber player playing for various groups across the United States, including Atlanta-based GremlinsDuo and Chicago-based Wei Zhongle, and as a classical musician with the New Chicago Chamber Orchestra, the Winston-Salem Symphony, Western Piedmont Symphony, and the Piedmont Wind Symphony.